According to an analysis by the global corporate growth consulting firm Frost & Sullivan's new report "Emergence of 3D Printing Materials", the global additive manufacturing formula market revenue in 2014 was $ 428.1 million, which is estimated to increase to 9.204 by 2020. One hundred million U.S. dollars.
As the field of application of 3D printing (or additive manufacturing) expands from prototype to final component manufacturing, related printing material suppliers are also beginning to develop specific material products for different applications instead of using one of the previous materials. Strategy in all areas. These suppliers have been keenly aware of the need to use better-performing materials to meet customer specifications, helping 3D printing to realize greater potential in directly manufacturing finished parts.
So far, system suppliers and chemical companies have introduced materials such as polyetherimide (PEI), polyaryletherketone (PAEK) and carbon fiber reinforced products and a wide range of high performance metal powders. However, to provide adequate support for feature manufacturing and mass customization for 3D printing, these vendors also need to go a long way in product innovation and differentiation.
According to a new report from the global corporate growth consulting firm Frost & Sullivan, "Emergence of 3D Printing Materials", the global additive manufacturing formula market revenue in 2014 was $ 428.1 million, which is estimated to increase to $ 920.4 million by 2020. .
Additive manufacturing has begun to take off in North America and Europe, as these areas are central to key industries such as aerospace, medical, dental and electronics, and these industries are leading the way in 3D printing applications. Similarly, China and South Korea are also expected to become hot spots for 3D printed materials and equipment manufacturing. In response, global chemical companies need to develop a viable long-term strategy, including the establishment of manufacturing plants in Asia.
“Although the opportunities are constantly expanding, the chemical industry is somewhat lagging behind, because most chemical plants that supply raw materials and formulations do not have a supply strategy specifically for the 3D printing market.†Frost & Sullivan's Industry Manager DeepakKarthikeyan. “This is mainly because the demand in the market is still relatively low, and the investment that suppliers need to make is relatively high.â€
In addition, 3D printing material suppliers, especially those offering formula services, have observed that even though current market demand is relatively low, the demand for technical support from system manufacturers and users is high. This forces suppliers to increase material prices. To mitigate the challenges of price and raw materials, solution providers need to find possible acquisition opportunities based on their product portfolio and market expertise.
Due to the increasing use of molten wire manufacturing and laser sintering technology in the industrial and consumer sectors, the demand for plastic wires and powders is also growing. At the same time, despite the relatively small market for metal powders, they still see an upward trend in demand from industries such as aerospace, automotive and medical, where direct metal laser sintering (DMLS) and electron beam melting (EBM) technologies are available. The application is also increasing.
“With the accelerated pace of concepts such as smart factories and digital manufacturing, 3D printing is expected to gain further traction in many end-user industries, driving demand for higher performance materials.†Karthikeyan noted: “The ability to provide a complete solution for end users. Suppliers will dominate the market as they are closer to end users and are well aware of market challenges."
As the field of application of 3D printing (or additive manufacturing) expands from prototype to final component manufacturing, related printing material suppliers are also beginning to develop specific material products for different applications instead of using one of the previous materials. Strategy in all areas. These suppliers have been keenly aware of the need to use better-performing materials to meet customer specifications, helping 3D printing to realize greater potential in directly manufacturing finished parts.
So far, system suppliers and chemical companies have introduced materials such as polyetherimide (PEI), polyaryletherketone (PAEK) and carbon fiber reinforced products and a wide range of high performance metal powders. However, to provide adequate support for feature manufacturing and mass customization for 3D printing, these vendors also need to go a long way in product innovation and differentiation.
According to a new report from the global corporate growth consulting firm Frost & Sullivan, "Emergence of 3D Printing Materials", the global additive manufacturing formula market revenue in 2014 was $ 428.1 million, which is estimated to increase to $ 920.4 million by 2020. .
Additive manufacturing has begun to take off in North America and Europe, as these areas are central to key industries such as aerospace, medical, dental and electronics, and these industries are leading the way in 3D printing applications. Similarly, China and South Korea are also expected to become hot spots for 3D printed materials and equipment manufacturing. In response, global chemical companies need to develop a viable long-term strategy, including the establishment of manufacturing plants in Asia.
“Although the opportunities are constantly expanding, the chemical industry is somewhat lagging behind, because most chemical plants that supply raw materials and formulations do not have a supply strategy specifically for the 3D printing market.†Frost & Sullivan's Industry Manager DeepakKarthikeyan. “This is mainly because the demand in the market is still relatively low, and the investment that suppliers need to make is relatively high.â€
In addition, 3D printing material suppliers, especially those offering formula services, have observed that even though current market demand is relatively low, the demand for technical support from system manufacturers and users is high. This forces suppliers to increase material prices. To mitigate the challenges of price and raw materials, solution providers need to find possible acquisition opportunities based on their product portfolio and market expertise.
Due to the increasing use of molten wire manufacturing and laser sintering technology in the industrial and consumer sectors, the demand for plastic wires and powders is also growing. At the same time, despite the relatively small market for metal powders, they still see an upward trend in demand from industries such as aerospace, automotive and medical, where direct metal laser sintering (DMLS) and electron beam melting (EBM) technologies are available. The application is also increasing.
“With the accelerated pace of concepts such as smart factories and digital manufacturing, 3D printing is expected to gain further traction in many end-user industries, driving demand for higher performance materials.†Karthikeyan noted: “The ability to provide a complete solution for end users. Suppliers will dominate the market as they are closer to end users and are well aware of market challenges."
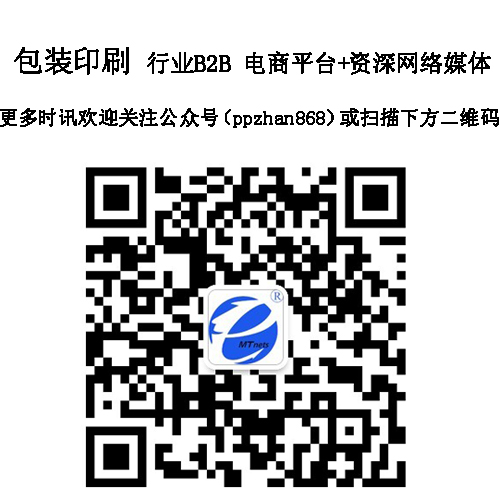
AC Hair clipper,ac hair trimmer,professional ac hair clipper,AC Trimmer
Zhejiang Hisun Electrical Appliance Co.,Ltd , https://www.cn-hisun.com