Whether the setting of the tension control parameters is reasonable will not only have a direct impact on the stability of the dry composite production, but also affect the subsequent processes such as slitting and bag making.
Tension initial setting
The initial tension setting is necessary for the dry compounding process and should be set by the operator before unwinding. The initial value of the tension should be set according to the characteristics of the substrate (thickness, surface tension, tensile strength, hardness, etc.) and the size and weight of the roll. In general, substrates with high tensile strength and hardness (such as BOPET film, PA film, etc.) need to set a substrate with relatively large initial tension and small tensile strength and high expansion ratio (such as For BOPP film, PP film, PE film, etc., the initial tension to be set is correspondingly smaller; the wider and heavier the roll, the larger the initial value of the tension.
Unwinding tension control
The unwinding tension control is divided into two sections, the first section is the tension control between the first take-up reel and the coating roller, and the second section is the tension control between the second unwinding reel and the composite roller. The constant tension is unwinding during unwinding, so the tension is kept substantially constant as the winding diameter is reduced. In addition, since the distance between the two segments is relatively short, the initial value of the set tension is smaller. It is worth noting that the heavier the coil, the greater the unwinding tension; when the coil diameter is the same, the wider the coil, the greater the unwinding tension.
Coating tension control
In dry composite production, the speed difference between the composite roll and the coating roll is varied by adjusting the current output to achieve the purpose of adjusting the tension of the intermediate dry portion (ie, the coating tension). In addition to the influence of the speed difference, the coating tension is also related to the elongation of the substrate, the thickness, the drying temperature of the dry composite equipment, the length of the drying zone, and the production speed.
The greater the elongation of the film, the easier it is to deform under tension. If the thickness of the substrate is not uniform, the pressure of the composite roll and the coating roll fluctuate, causing an abnormal change in the composite speed and also causing tension control. influences. If the coating tension is too small or there is no tension, that is, the speed of the coating roller is greater than or equal to the speed of the composite roller, the coating effect of the adhesive is affected, and the composite film may wrinkle or even cause film accumulation. However, the coating tension should not be too large, because the tension is too large, the tension will be too large, and the film will undergo irreversible tensile deformation under heat, and even longitudinal "wrinkles" will eventually cause a large amount of scrap of the composite film.
Therefore, attention should be paid to the matching of the coating unit tension. Whether the tension is matched mainly depends on whether the tension control of each layer of the substrate is coordinated, whether the tension setting is appropriate, and whether the degree of retraction of the film after the dry compounding is consistent. Except for paper and aluminum foil, most of the substrate will undergo some deformation and rebound under tension, especially after high temperature drying. Taking a PE/Al/PET composite film produced by a certain batch of our company as an example, after dry compounding, the edge part and the middle part of the PE/Al/PET composite film are delaminated, which is a typical “tunnelâ€. phenomenon. After analysis, this is because the tensile strength of the PET film is small. When the coating tension is too large, it is easily deformed after being heated, and the tensile strength of the aluminum foil is large, and the elongation ratio is higher than that of the PET film. Small, the rebound degree of the two is inconsistent, so the aluminum foil is heated and raised to form lateral wrinkles. When the second compounding process is carried out, the PE film shrinks under low temperature cooling after being stretched, and the relative sliding between the base films occurs especially when the adhesive is not completely crosslinked and cured. , causing wrinkles, "tunneling", delamination and other issues. Therefore, in the dry compounding process, the current output should be appropriately adjusted for the characteristics of different substrates, and the speed difference should be changed to obtain a suitable coating tension value.
Winding tension control
The purpose of the winding tension control is to achieve the best winding state of the finished composite roll. The winding tension control has three forms of constant tension control, constant torque tension control and taper tension control. The three characteristics are as follows.
(1) Constant tension control. Constant tension control has a narrow adaptation range. In order to prevent the phenomenon of partial roll, eccentricity and hard roll during winding, this method is only suitable for coils with small coil diameter.
(2) Constant torque tension control. The application of constant torque tension control is not particularly common, because the larger and heavier the winding diameter of the coil, the greater the winding tension, and the torque required at this time is also large. Therefore, the constant torque tension control is only suitable for medium-volume coils and dry composite production with large substrate elongation.
(3) Taper tension control. Production practice has proven that the use of taper tension control is the best choice for good winding. The taper is the attenuation rate of the winding tension which decreases with the increase of the winding diameter at the time of winding, and has a linear taper and a curve taper. Straight taper means that the winding tension decreases linearly with the increase of the winding diameter; the curve taper is the tension curve set in a relatively idealized state. The taper can be adjusted according to different materials, different thicknesses, and different soft and hard substrates. In general, thick and hard substrates have a small taper value and a soft substrate has a large taper value.
The winding tension control should also be of appropriate size. Under normal circumstances, the composite film should be sufficiently cooled before winding, so that the composite film is well shaped and the cohesive force of the adhesive is increased. If the composite film is not completely cooled, the winding will be too loose or the material roll will be loose. The base film will slide relative to the adhesive because the adhesive is not fully crosslinked and solidified, and the cohesion is small. The film roll is tightened. However, it is worth noting that the winding tension should not be excessively increased. Otherwise, the coil will be curled due to the tightness of the inner pine or the inner layer will wrinkle, which will not only affect the appearance, but also affect the use of the composite film.
The tension control of the dry laminating machine has an important influence on the performance of the composite membrane, and it is a problem worthy of further study and discussion. The key to the tension control of dry laminating machine is to fully consider the coordination of the properties of the substrate, the characteristics of the adhesive and the environmental conditions. In addition, operators should dare to try and sum up in actual production in order to obtain reliable and accurate control methods, so as to better control the tension and obtain a composite film with high quality, good performance and flat appearance.
The above content is reproduced in the "Printing Technology" official WeChat (Printech1957), authorized by the company to publish, copyright, piracy will be investigated!
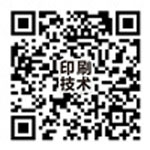
Design Furnitures,Furniture Modern,Modern Furniture Intdoor,Furniture In Small Spaces
BOSA FURNITURE CO.,LTD. , https://www.bosafurniture.com